デジタルトリプレット(デジタルツイン+ノウハウ)
デジタル空間で生産現場を再現し、改善施策のトライ&エラーを検証します
コロナ禍などの不測の事態や、かつてより速いスピードでの需要変動の中で、工場やラインなどの生産領域も迅速に変化し続けることが求められています。しかし、それらの生産領域での改善施策のトライ&エラーはコストの観点から数多く実施することはできません。
そんな時に活用できるのが、デジタル空間です。オーツー・パートナーズは、現場のノウハウの標準化、実世界の装置から取れるデータ、デジタル仮想空間上での検証の3つを組み合わせたデジタルトリプレットで、生産現場の生産性向上に貢献します。
デジタルトリプレットとはデジタルツインに、ベテラン技術者の知恵・日々のカイゼンなどのノウハウや技術を取り入れたもの。お客さまがすでに保有しているリソースを最大限活用し、急速な需要変動に対応できるよう支援します。
たとえば既設ラインであれば、在庫、生産要求、設備能力、シフトなどの実績をデータとして取り組み、生産計画の最適化を図れます。新設の工場やラインを検討する際には、設備やオペレーターが不在の段階から、仮想空間を使って最適なレイアウトを検討できます。
※デジタルトリプレットの詳しい解説はこちらのコラムをご覧ください。
こんな課題を感じていませんか?
- 生産計画の変更に迅速に対応できるようにしたい
- 誰でも生産計画立案を実行できる仕組みにしたい
- 工場の新設を計画しているが、最適な案なのか検証したい
現場の生産性向上のためには、すべての工程でベテランの知見をデジタル化することが重要です
ただ「生産性を向上する」というだけではゴールがあいまいで、成果に結びつきにくいことがあります。QCD-Rや生産柔軟性、あるいはC.N.対応など、何を重要視するかを生産現場のみならず、経営戦略の視点も交えながら定義します。
部品納品のタイミングや在庫管理、品質検査工程のレイアウト、製品在庫と出荷のタイミングなど、生産の現場ではすべての工程が影響し合っています。全体に適合した生産性向上を図るためには、モノ・人・情報の流れやタイミングを可視化し、人の判断によりばらつく箇所を抽出する必要があります。ばらつきを低減するために、ベテランやエースの知見を紐解き、オペレーションへ標準化します。
効率的に生産現場を改革していくためには、すでにあるオペレーターのナレッジや蓄積したデータを活用することが重要です。オペレーターのナレッジや装置のデータをシミュレーションモデルに関連付け、実際の生産現場において活用できるシミュレータの環境を整備します。
オーツー・パートナーズが選ばれる理由
理由01 現場のナレッジを形式知化した実績
オーツー・パートナーズは創業以来、製造業の暗黙知の形式知化を支援してきました。経験豊かなメンバーが、効果的な手法を用いてお客さまのお手伝いをします。生産現場におけるモノ・人・情報の流れを可視化し、暗黙知化しているポイントを導出、ヒアリングを通してナレッジを形式知化します。生産現場で属人化している勘・コツが形式知化されるので、技術の伝承につながります。
理由02 経験豊富なメンバーがデータ収集環境を構築
生産性向上の検討に必要な生産データや装置データを収集するシステムの選定・構築が可能です。当社には製造業において、同様の業務を経験してきたメンバーが多数在籍しています。
自社でデータ収集環境を構築するリソースがない場合でも、お客さまに代わって、オーツー・パートナーズがデータ収集環境構築を実行します。
理由03 独自のナレッジ×デジタルソリューションを提供
エースやベテランの知見を形式知化したうえで、仮想空間で検証できるようCAEモデルのロジックに実装します。当社のコンサルタントには元技術者のメンバーが多く、暗黙知の形式知化と、デジタル技術・IT技術の両方を得意としています。お客さまの生産現場と整合性の取れた仮想空間を用意できるので、最短時間でデジタル・トリプレットを活用できます。
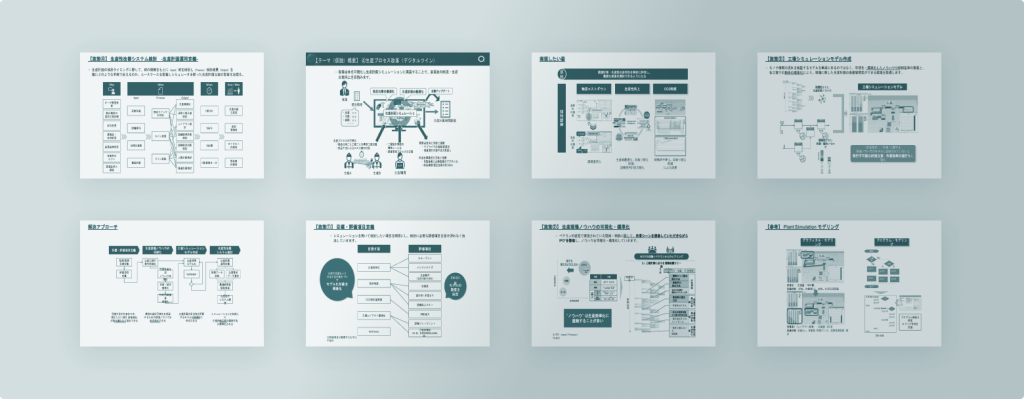
支援事例
モデルケース① 実際の生産工程では試せない施策を仮想空間で確認
社名 | 産業機器メーカー |
課題 | 抽象的な生産計画しかなく、生産性が高いのかどうかも判断できない。 |
施策例 |
|
成果 | 個別工程が別の工程へ与える影響を各担当者が理解し、全体最適の生産現場改善を考えられるようになった。また実際の生産工程では試せない施策を仮想空間で確認し、目途が付けられた。 |
モデルケース② 業務を平準化しベテラン以外も検証可能に
社名 | 大手飲料メーカー |
課題 | 最適なライン構成なのかがわからない。過去の仕様を踏襲したライン新設しかできない。 |
施策例 |
|
成果 | 設備仕様における「こうあるべき」という暗黙のルールが本当に正しいのか検証できた。また、段取り替えタイミング、保全タイミングなど、さまざまなパターンをベテラン以外も検証できるようになったので、業務の平準化につながった。 |
プロジェクトの進め方
アプローチの一例を紹介します
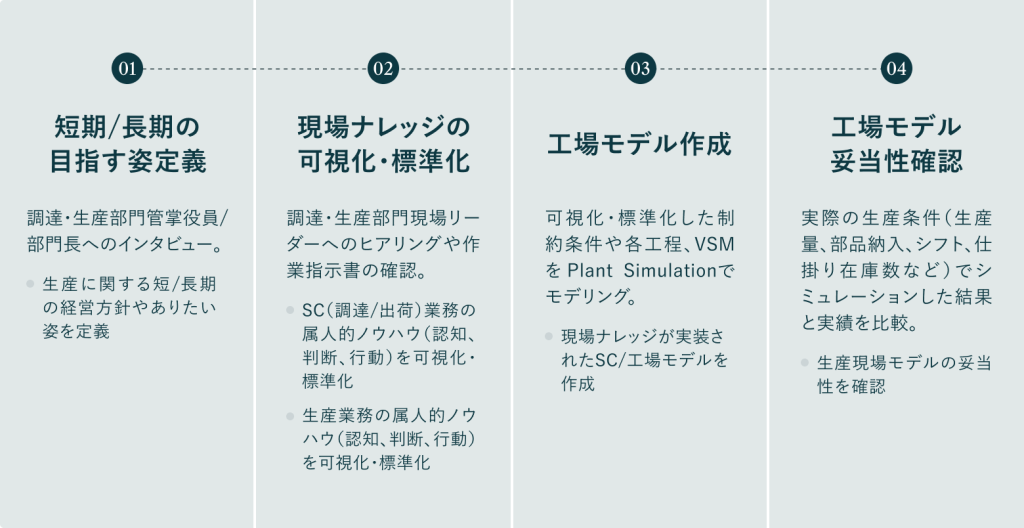
大企業から中小企業、地方のスタートアップ企業まで、
幅広い支援事例から代表的なものを紹介いたします。