モジュラーデザイン企画・推進
徹底的な業務分析をもとに、MDを定着させる仕組みをつくります
オーツー・パートナーズは設計から生産技術/生産準備、製造、保守保全に至るエンジニアリングチェーンでのMD実装を得意としています。MDは手段であり、型に当てはめて実装するものではありません 。お客さまの日々の設計や生産手順を丁寧に分解して再構成すれば、どのような業界・業態であってもMDは実装できます。
当社はお客さまへの徹底的なヒアリングをもとに、業務を分析します。そして上流から下流まで部門をまたいでプロジェクトを推し進め、MD定着による品質の高位平準化や設計工数の削減、調達工数の削減などを実現します。
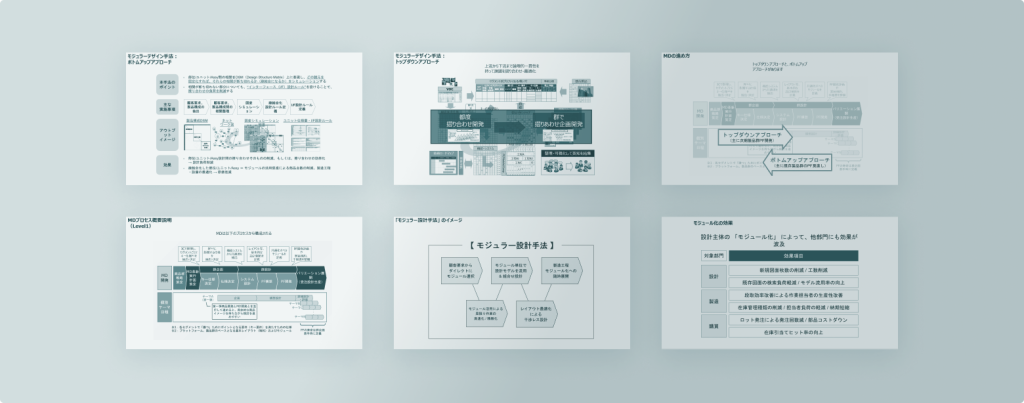
こんな課題を感じていませんか?
- 設計ルールが形骸化し、流用設計が常態化している
- 設計業務の属人化が進み”似て非なる”亜種が大量に発生している
- 製品が複雑すぎて全体を把握している技術者がいない
- 個別受注(専用設計/一品一様)製品なのでモジュール化できない
MDへの変革は設計部門だけでは実現できません
MDはエンジニアリングチェーン全体に関わる施策です。成果を上げるには生産技術やサービスなどエンジニアリングチェーン下流へまたがることが不可欠です。またエンジニアリングチェーンの途中から実施すると、上流との整合が取れず手戻りが発生することもあるため、MDを実装するチームは部門横断型で組成するべきです。MDに関わる部門の代表者もメンバーにふくめ、MD施策が「設計部門の便利ツールつくりプロジェクト」となることを防ぎます。
MD実現のためには、ベテラン社員の協力、そして自身の経験やノウハウを語れる人材が欠かせません。MDプロジェクトで「既存設計の紐解き」から「過去製品の棚卸し」を進めるためには、これまでの設計手順や思想を明らかにすることが必要だからです。このプロセスによってお客さまのものづくりのコア部分を残しつつ、MD化を実現していくことができます。
MDは自社のものづくりをゼロにリセットするプロジェクトではありません。熱意をもった若手・中堅社員がベテラン社員と一緒にMDに取り組むことで、自社のコア技術を継承するだけでなく、新たなものづくりの土台を自分の手で構築していく経験を積めます。このため自身の業務を改革しようとする意志をもった、将来の会社を担う人材が必要です。
オーツー・パートナーズが選ばれる理由
理由01 実務経験者が導入後の業務変化を具体的に提示
MDはエンジニアリングチェーン全体に影響が及ぶため、MDの定着と成果の創出には関係者の協力が欠かせません。そのため具体的な施策を始める前に、すべての関係部門から業務内容とお困りごとをヒアリングします。業務分析をもとにMD導入後の業務変化を具体的に描き、そのために必要な打ち手を提案します。
当社にはエンジニアリングチェーン各部門で実務経験のある元技術者が多数在籍しており、自身の体験をもとにお客さまの悩みをすばやく深く理解できます。プロジェクト初期には関係部門と丁寧に対話する場を設け、相手の立場を理解しながら、MDを「自分事」として捉えられるように働きかけます。
理由02 MD定着に最適なツール導入から仕組みづくりまでサポート
MD定着のカギは「ルールを使わないと設計できない仕組み作り」 にあります。時間をかけて作成したルールをExcelにまとめて共有しても、設計者はすぐに参照しなくなります。CADや自動化ツールにルールを組み込み、それらを使わないと仕事が進まない状況をつくることが重要です。この仕組み作りを実現するために、当社がソフトウェアの選定から実装と定着までを支援します。一般的にソフトウェアの選定には多くの手間と時間がかかります。当社がサポートすることで選定にかかるコストを削減し、定着までの時間を短縮できます。
理由03 独自のツールでMD導入の実績をいつでも定量化
MD導入前の投資対効果の予測も重要ですが、施策後の実績を定量化することにこそ意味があります。設計の複雑さがどの程度解消されたか、設計にかかる工数が何時間削減できたか、製造治具はどれくらい共通化できたかなど、コストに関わる指標を定義し、MD導入の前後で評価を行ないます。当社はこれまでの支援ノウハウを反映した独自の設計整理構造化ツールや、お客さまの業務分析のためのツールなどを持っており、施策前後の効果を容易に算出できます。長期にわたるMD施策の途中段階でも定量化が可能なため、経営層に求められたタイミングで実績を提示できます。
支援事例
モデルケース① MD施策への投資を2年半で回収
社名 | 自動車部品メーカー |
課題 | オーダーごとに専用設計を実施しているため、開発工数や販管費など個別部品費以外の原価比率が大きく利益率が上がらない |
施策例 |
|
成果 |
|
モデルケース② 設計工数と調達コストを大幅に削減
社名 | 半導体メーカー |
課題 | 顧客の細かなオーダーに応えるうちに似て非なる亜種が大量に発生している。また差分設計中心のため、設計ノウハウの蓄積が少ない。 |
施策例 | 顧客や製造時期のトレンドが見られたため、過去製品の棚卸し時に機能領域や仕様などの分析と情報整理を実施し、オーバースペックでないかなどを検討。 |
成果 |
|
モデルケース③ MDを構築し設計工数を半減
社名 | 重工メーカー |
課題 | 個別受注型産業のため、設計者の裁量が大きく亜種が発生。また製品サイクルが長いため、過去設計の思想が引き継がれにくい。 |
施策例 | 変化点が発生しないユニットと変化点が生じるユニットに大別し、粗いモジュールと詳細モジュールの2階層構成のMDを構築 |
成果 | 設計工数50%削減 |
プロジェクトの進め方
アプローチの一例を紹介します
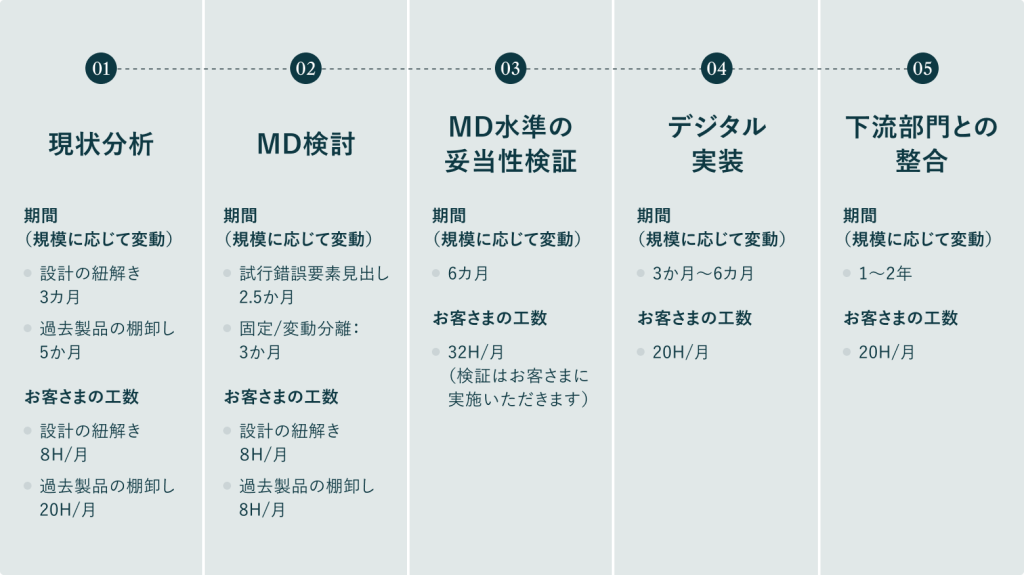
大企業から中小企業、地方のスタートアップ企業まで、
幅広い支援事例から代表的なものを紹介いたします。