【機械設計・寄稿転載】個別受注型開発におけるルールベース設計システムの構築・活用方法
- テクノロジー
- コンサルティング
- 製造業
- ものづくり
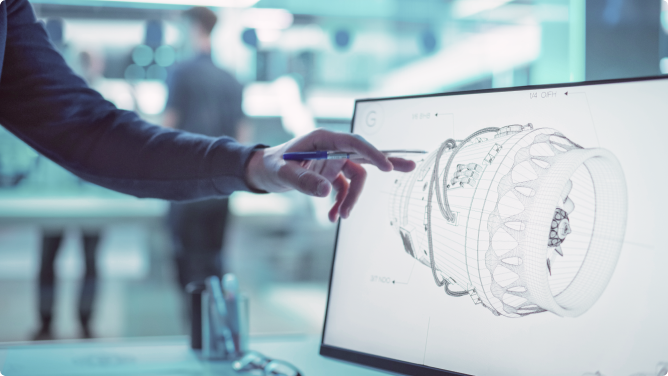
目次
本コラムは雑誌『機械設計2023年8月特別増大号』(日刊工業新聞社)に寄稿いたしました記事の転載となります。下記リンクよりバックナンバーが購入できます。
機械設計 2023年8月特別増大号 – 日刊工業新聞社 公式オンラインショップ|Nikkan Book Store
1.個別受注型開発における現状の悩み
“製品の複雑化”・“顧客要求の多様化”・“製品ライフサイクルの短期化”が顕著になってきているなか、日本の製造業はより一層ビジネスに対する俊敏性を高めなければならないと強く感じる。特に、個別受注型開発のビジネスにおいては次のような現状であり、技術者ひとりひとりの努力で達成しうるものではない。顧客満足度アップや市場での競争力保持のために都度設計が必要と思っている。
- 開発期間の短期化により、設計ロジックを理解しない流用設計が増えている
- 技術を流用するという視点での根拠に遡った設計はできていない
- 現場レベルで発生する品質問題の解決に多くのリソースが割かれている
- 関係会社等のリソースで設計を回す場面が増えてきている
また労働力の確保も困難な状況のため、製品開発を正確に、迅速に、効果的に実施するには従来の“型“から離れ、設計・開発プロセスの改革が必要である。
2.製品特性ごとの設計・開発プロセス改革の方向性
紋切型で設計・開発プロセス改革の“べき論”を語っても意味がなく、製品特性や将来自社のビジネスをどういった方向に持って行きたいかにより分けるのが良い。例えば、自社仕様に誘導していくことを指向する場合には、部品やユニット、生産手段までも標準化を行い仕様の変動要素を極力減らすことが考えられる。メリットとしては、製品原価を大幅に低減できるうえ生産効率もあがるので、コスト競争力をもつことができる。一方で、顧客にとって魅力的な要素(機能・価格・納期・信頼)がなければ見向きもされない製品となってしまう難しさはある。そのようなことを回避するため、大局的な考えではあるが、変動要素を増やし顧客対応力を強化するという方向性もある。この場合、解析を利用し試作・検証の数を減らすなど都度対応力の向上は必須となる。またこれらの折衷案のような考えだが、複数バリエーションを用意しておき要求に応じて最適な構成を組合せ・選択する、といった方向性もある。
いずれの方向性にせよ自社製品の設計根拠(ロジック)、意思決定の仕方を明確にして標準化・ルール化することが改革の起点であり、それらを活用し設計の一部を自動化することで俊敏性はあがっていく。これがルールベース設計の根幹であると我々は捉えている。
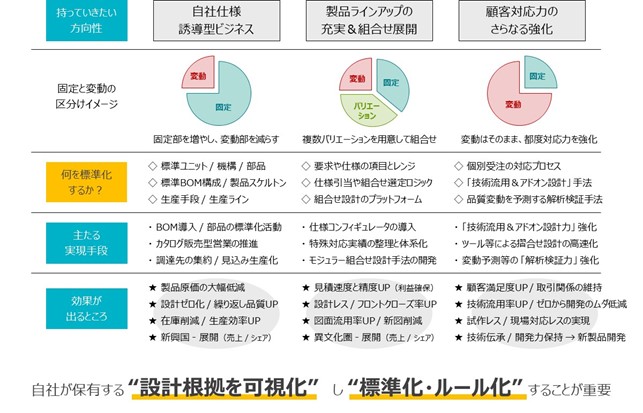
3.ルールベース設計のコンセプト・概要
ルールベース設計、設計自動化という言葉から “技術者が考えなくなる“ という印象を持たれる方がいらっしゃる。しかしルールベース設計、設計自動化の本質は、検討の抜け漏れや人手による情報の検索・転記といった作業のムダを抑制でき ”技術者がより考えるようになる“ ことである(日本人は慮る力が格段に高く、これを活用しない手はない)。
ルールベース設計を端的に表現すると、熟練技術者やエースエンジニアが持っているノウハウや知見を形式知化・標準化したものを設計ルールとして活用することである。ここで大事になってくるのがルール化された設計根拠や意思決定の仕方は活用するが、いま取り掛かっている設計・開発内容の決定は技術者が考え実施するということである。なぜならば、製品への要求が多様化・複雑化しているのでトレードオフ関係の設計要素も多々あり、何を優先し何故このような設計にしたかは最終的に人が判断するのが望ましいからである。
4.ルールベース設計の活用例・効果
本章では活用例と効果について2つ事例を述べさせてもらい、より興味をもっていただいてから次章以降でルールベース設計の詳細について触れていきたい。
1つ目は、見積対応速度および見積精度の向上に活用した事例について紹介する。ルールベース設計を実施される以前は、顧客からの見積依頼に対して都度基本設計をおこない、外製品や調達品のコストを把握するため設計図書も新規に作成されていたため、見積作成に約1カ月時間を要していた。また設計思想も標準化されていなかったため、設計者による差もあり見積精度も高くはなかった。このような状況からの脱却を目指し、顧客からの要求仕様を入力すると知見を反映したルールに則り自動的に設計案が提示され、回帰分析により導出された部品コスト情報と合わせて候補案のなかから技術者が最終決定するルールベース設計を取り入れた。その結果、以前は約1カ月要していた見積回答が1日で実施できるまでスピードアップしたのである。
2つ目の事例は、顧客要望を伺いながら自社仕様を提案する事例についてである。顧客要望に応えることで市場優位性を保てていると強く考えており、その結果製品仕様が増え続け、部品やユニットの共通化も進んではいないといった悩みを抱えている企業は少なくない。共通化が進まないと調達・製造コストの低減も難しく、競合他社に比べて利益が出にくい構造になってしまう。そこでルールベース設計を適用し、顧客との商談段階で要求仕様を伺いつつその場で基本設計を行い、過去製番との比較検証をして近しい構成を提案するという業務プロセスに変革を行った。得られた効果としては、部品・ユニットの共通化による収益性改善のみならず、生産における習熟度も高まるので製品品質も向上する。
この事例以外にも得られる効果はあり、それらが連鎖しまた新たな効果を生み出す好循環がおこる。ゆえに、ルールベース設計は設計部門だけの取組みに留まらず、営業部門や生産部門にも範囲を広げることで得られる成果は大きくなる。
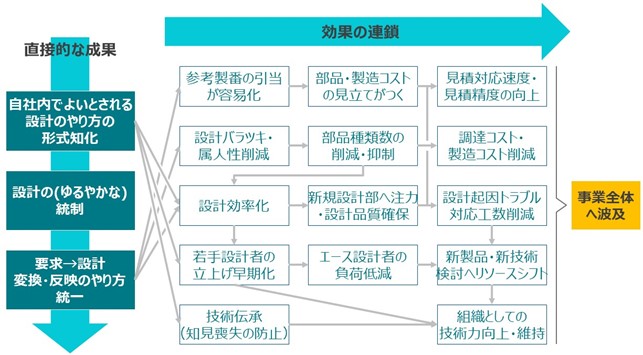
5.ルールベース設計環境の準備・システム構築
ここまでルールベース設計の概要や活用例・効果について述べてきたが、本章ではルールベース設計環境の準備からシステム構築まで深堀していきたい。システムまで何故含めるのかというと、ルールを集め書籍化したものを設計時に人手で確認・活用する運用にしてしまうと享受できる効果が小さくなってしまうからである。このような部分はデジタル技術を活用し効率的に進めていかれることを推奨したい。
最初にルールベース設計環境整備の全体像からみていきたい。環境構築は大きく5つのステップで構成される。
- 業務プロセス(主に設計手順)整流化
- 設計可視化(インプット/プロセス/アウトプット/設計諸元/誤差因子の関係可視化)
- 設計ロジック定義
- 設計標準化・ルール化
- システムへのルール実装・関連ツールとの連携構築
(②と③を纏めて設計の形式知化と称する場合もある)
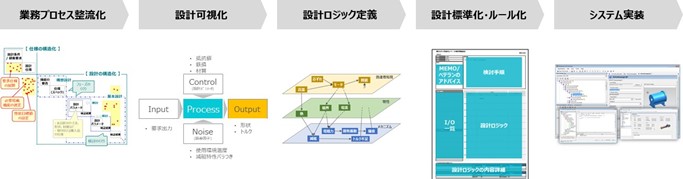
まず➀業務プロセス整流化だが、ここがルールベース設計の骨格を決める部分になる。ルールベース設計はその名の通りルールに準じて検討を進めるので、何から検討を始めるのか、そのために必要な情報は何か、その情報はどの業務からもらうのか、その検討結果を継続するどの検討に活用するのかが明確に定義されなければならない。意外かもしれないが、この部分が人によるばらつきが一番多い。整流化自体は、設計構造マトリクス(Design Structure Matrix※1)などを使用して設計の手順を可視化し手戻りが少ない順番に入れ替えたりして行う。
続いて②設計可視化は、検討(Process)に必要な入力情報(Input)と検討により導出される情報(Output)に加え、誤差因子(Noise)と設計パラメータ(Control)を関連付けて整理する(IPONC整理)。ここでポイントになるのが、最初から設計要素全てを可視化しようとすると途方もない作業になり完成前に頓挫してしまうので、➀業務プロセス整流化の結果から、顧客が優先する要求性能と関連の強い領域にまずは対象を絞って可視化していくことである。
そして③設計ロジック定義は、②で可視化された検討要素の繋がりから設計思想や根拠をもとに設計ロジックを明確にする。この段階では技術者により思想や根拠が異なっていても、次の工程で標準化をするので問題ない。
一番の山場である④設計標準化・ルール化では、複数の技術者の設計思想や根拠をもとに今後どの設計ロジックをベースとするのかを議論し決定する。ここでは何故その設計ロジックをベースとするのか、蓄積してきた知見だけでなく物理メカニズムにまで立ち返って議論することが大事になってくる。ベテラン技術者に忖度したり、声の大きい人の意見に流されたりしてはいけない。
最後に選定したシステムに標準化された設計手順やルールを実装する。この際に、ルールのもととなった根拠が確認できる仕組みや、ルール更新のし易さなどを加味してシステムを選定していただきたい。また設計を支援する内製の計算ツールやCAE、CADとの連携も構築しておくことで活用の範囲が大きくなる。
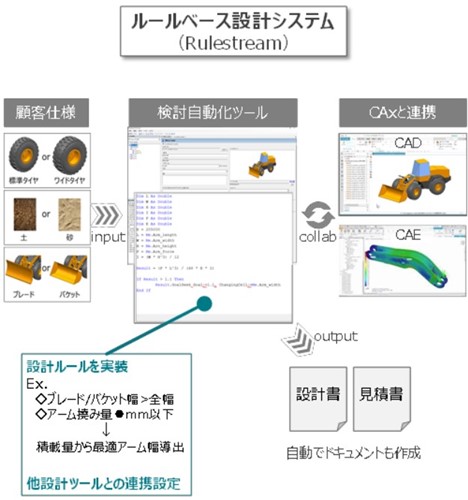
6.ルールベース設計システムの応用展開
前章でCADやCAEといった設計支援ツールとの連携について言及したが、応用展開としてPLM(Product Lifecycle Management)との連携についても紹介したい。ルールベース設計システムとPLMが連携することで、例えば標準構成(Maser-BOM)をPLMより読み込み、顧客仕様に応じてカスタムした部品・ユニットを更新し新たな製番としてPLMに登録、管理することになる。この機能により、参考とした標準構成との繋がりや設計変更履歴も追跡できるので、主機能・副機能を区別しながらバージョン管理が円滑に行えるようになる。
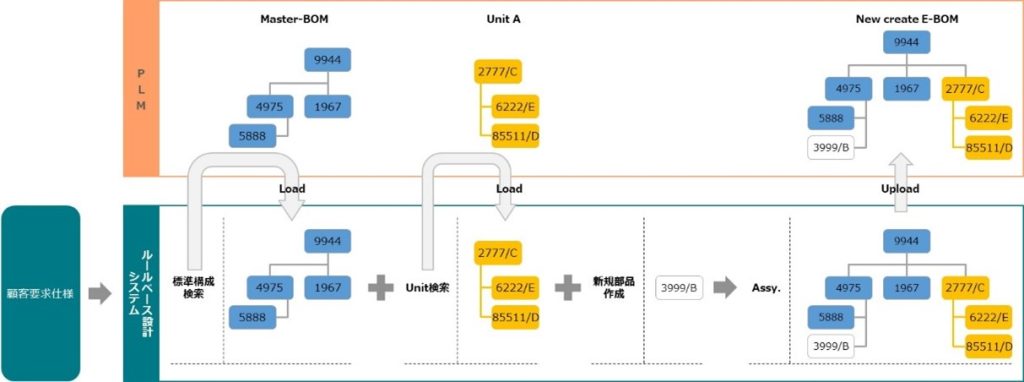
また他の応用方法として、顧客要求を入力する部分と検討結果を出力する部分だけ利用できるように制限をかけ、ルールの中身をブラックボックス化することで機密性を担保しつつ様々なユーザーに利用してもらえることができる。具体的な例だと、海外現地法人の営業担当が商談時にThin Client端末から要求仕様を入力し、サーバー上のルールベース設計システムから導出された設計結果あるいは見積書を即座に提示することが可能となる。従来であれば設計ロジックは秘匿性が高く海外現地法人へは開示できないため、都度日本側へ問い合わせが発生していた。そのため回答までの時間がかかるだけでなく、日本側技術者の検討時間も発生していたが、それが極限にまで減らせるのは大きなメリットになり得る。
7.総括
繰り返しにはなるが、ルールベース設計の根幹は設計根拠を形式知化・標準化しルールとして活用することである。長年の製品開発を通して培った知見、特に試行錯誤や調整を繰り返してこられた “擦り合わせ” 部分を丁寧に紐解くことが肝要である。ここは大変骨の折れる作業ではあるが、技術を伝承していくという観点にとっても大切なことであるのでしっかりと行っていただきたい。
今回紹介したルールベース設計システムが全てではないが、技術者の方々には作業時間※2を減らし、思考の時間※3を増やす取り組みを継続して実施いただくことを切に願う。そして顧客への提供価値を高めてもらい、各社が顧客にとってなくてはならない存在になっていただきたい。
1
デザイン・ストラクチャー・マトリクスDSM:複雑なシステムの可視化とマネジメント
著者;スティーブン・D・エッピンジャー, タイソン・R・ブラウニング
出版社; 慶應義塾大学出版会
発行年;2014年
2 作業時間;図面を作図する、技術計算をする、生産指示書を作成する時間
3 思考の時間;情報から判断をする、制約条件の重要度を検討する、潜在的顧客ニーズを探索する時間