デジタル化を見据えた全社的な業務改革で競争力強化と組織変革を実現
支援内容 |
|
---|
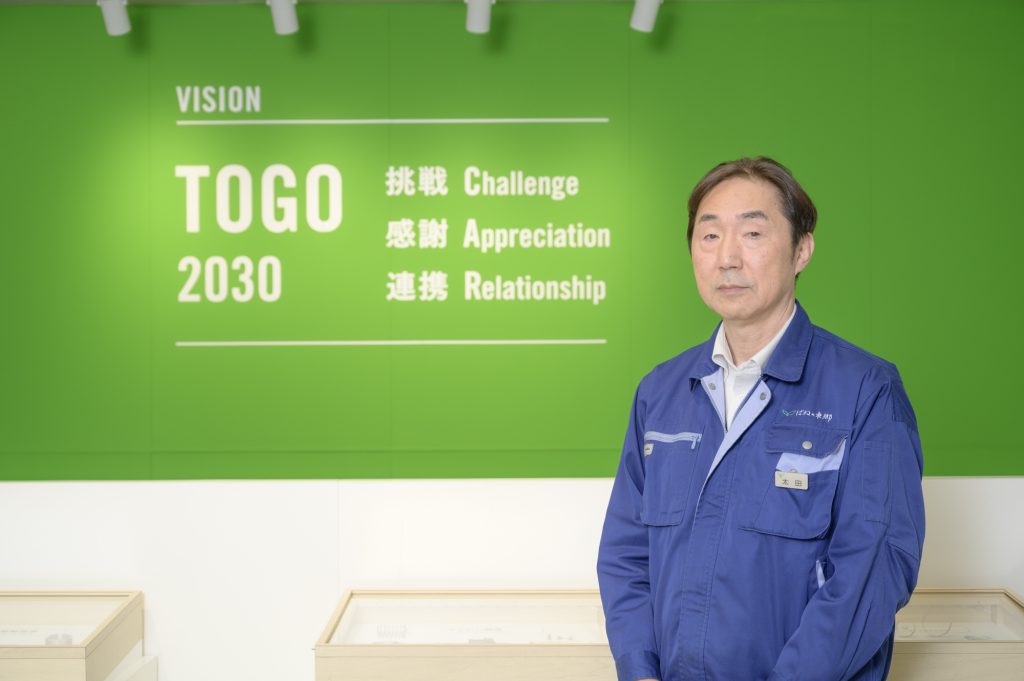
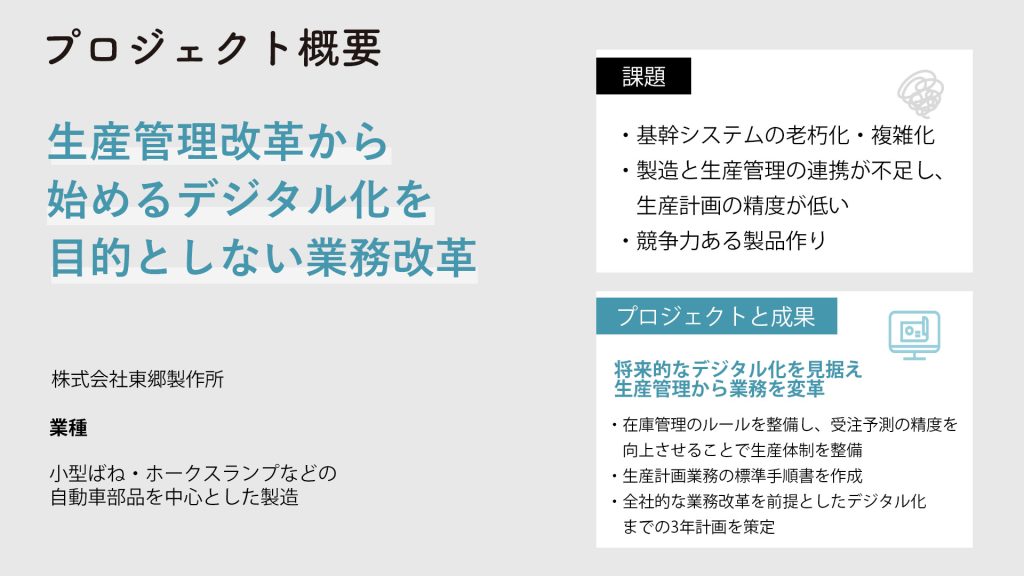
株式会社東郷製作所(以下、東郷製作所)は、小型ばねを中心とした自動車や産業機械向けの高精度な製品を製造する企業です。創業以来、確かな技術力を強みに多くのメーカーから信頼を獲得してきました。
今回、長年使用してきた基幹システムの老朽化をきっかけに、工場のDX化による競争力向上を目指してオーツー・パートナーズが支援に入ることとなりました。企業がDXを推進する際、「デジタル化が目的」となってしまうと形だけのデジタル化となり、狙いの効果が創出できないケースが多々あります。そこでまずは業務変革を起こし、そのうえでシステム化を進める、「XからのD」のアプローチが重要です。生産管理改革や部門間の連携といった主要課題の改善活動と、それに伴う社内の意識変化について、東郷製作所デジタル推進部部長・太田貴也氏に伺いました。
【お客様からのコメント】
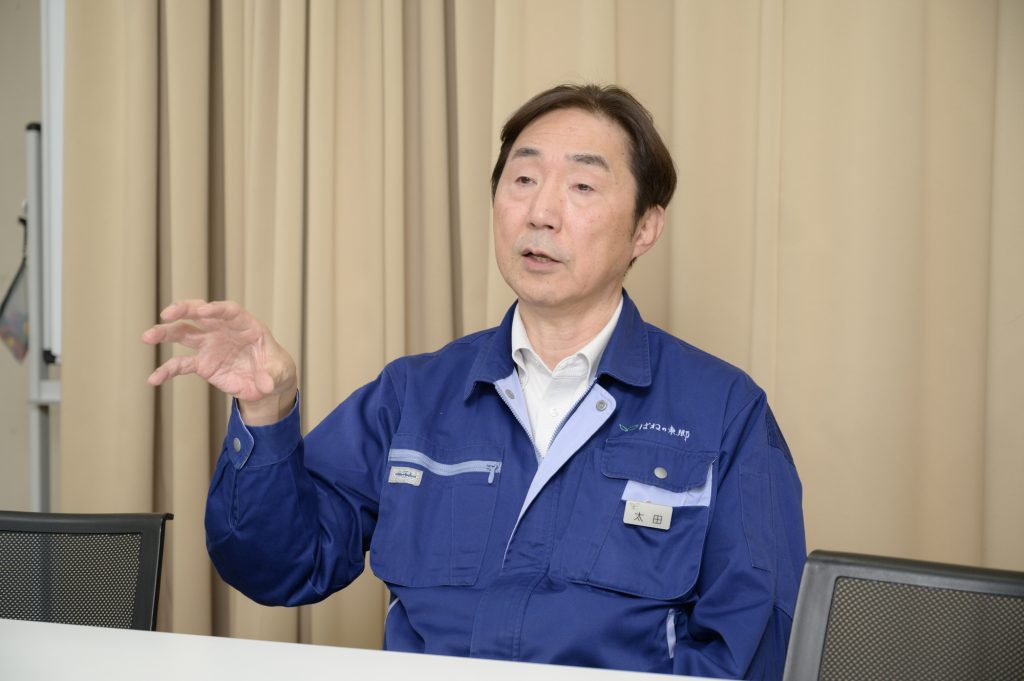
「オーツー・パートナーズが支援に入る以前は、各部署が意見を出し合っても、議論がまとまらず、合意形成に至らないケースが多くありました。しかし、ゴールへの明確な道筋が示されたことで、『この活動を進めることで仕事が大きく変わるのではないか』という期待感を持つようになり、担当者レベルでも意識が大きく変わりました。結果として、プロジェクトに前向きに関わる社員が増えました」(太田氏)
【ご支援先】
株式会社東郷製作所
株式会社東郷製作所は、愛知県東郷町に本社を構える、1881年創業のばねメーカーです。1940年に小物ばねの製造を開始し、自動車用部品の小物ばねや電子関連部品などを完成車メーカーをはじめ、サプライヤー各社にも供給しています。特にホークスランプ分野では国内トップシェアを誇ります。「『昨日よりもよい品』で社会に奉仕する」を社是とし、高品質な製品を提供し続けています。
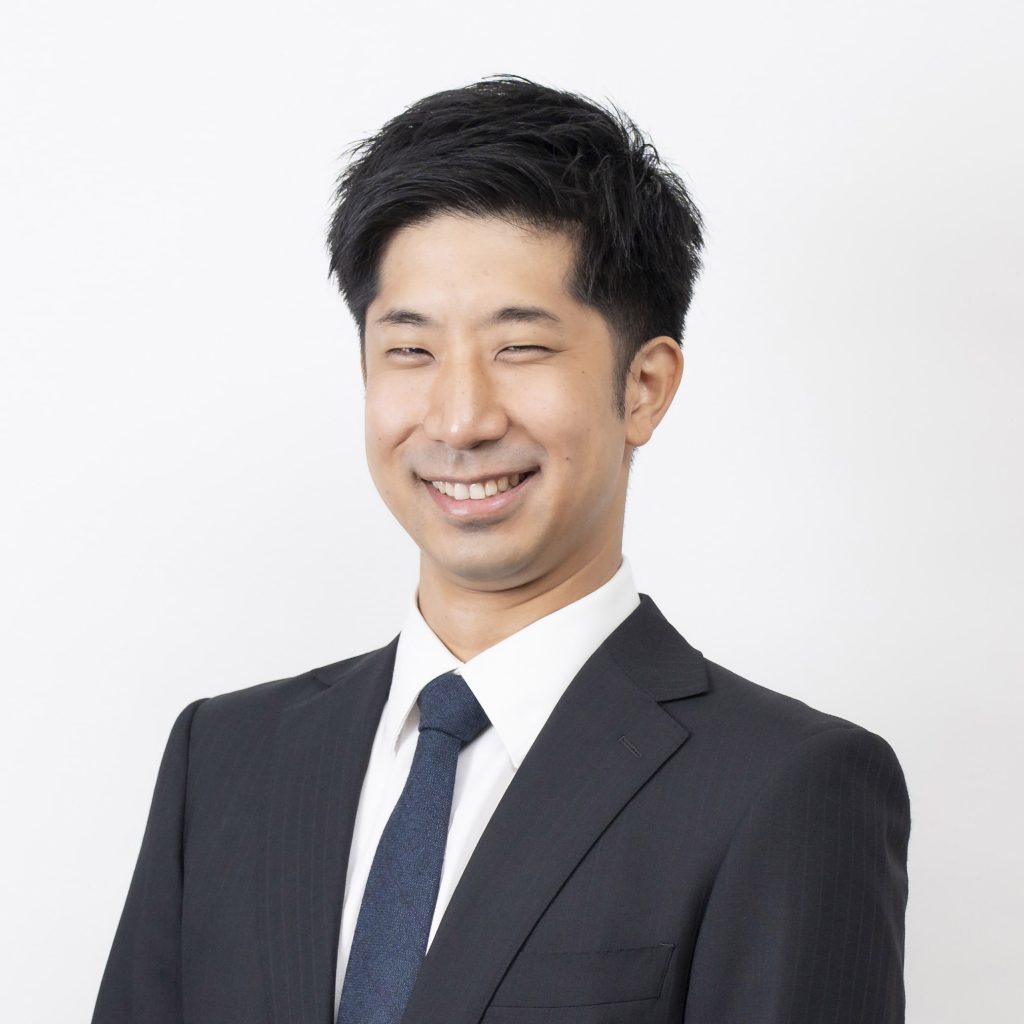
担当プロジェクトマネージャー
林 貴文
株式会社アイシン出身。工場品質管理部門にて、不具合対応から新製品立上げ・原価低減活動などに従事。その後、オーツー・パートナーズに参画。
生産・製造領域を得意としつつ、設計などの上流側との連携まで考慮したコンサルティングを実施。直近では生産現場アセスメントを起点としたDX計画策定・実行までの一貫支援や、サプライチェーン可視化によるリードタイム最適化支援などの改革を担当。
全社的なデジタル化を見据えた工場全体のアセスメントからスタート
長年にわたり、小型ばねを中心とした製品を製造してきた東郷製作所ですが、DXの推進は大きな課題の一つでした。特に、基幹システムの老朽化が深刻で、長年にわたる使用の中で機能が次々に追加され、複雑化していました。また、使い勝手においても、個人依存する傾向が強まっていました。こうした状況を改善するため、基幹システムの刷新を進めるプロジェクトがスタートしました。
「過去にも、社内だけで進めたプロジェクトが頓挫することが多々ありました。各部署がそれぞれの立場からの主張に終始し、議論が収束せずにプロジェクト自体が立ち行かなくなるのです。そこで今回は、外部の専門家の協力を得ようと考え、オーツー・パートナーズに支援を依頼しました」(太田氏)
プロジェクトは、生産プロセスにおけるDXの進行度や課題を網羅的に評価するアセスメントサービス「MaPDM-A」からスタートしました。MaPDM-Aは、アセスメントを起点に、各業務の問題構造の整理やDXグランドデザインの立案、実現シナリオ作成までを1〜2か月で行う、オーツー・パートナーズ独自のソリューションです。工場の全体最適を実現するために、網羅的に生産機能の分析を行い、目指すべき姿を明確にします。また、部門横断で問題点の因果関係を紐解くことで、解決すべき問題点を明らかにしたうえで改革シナリオを策定していきます。
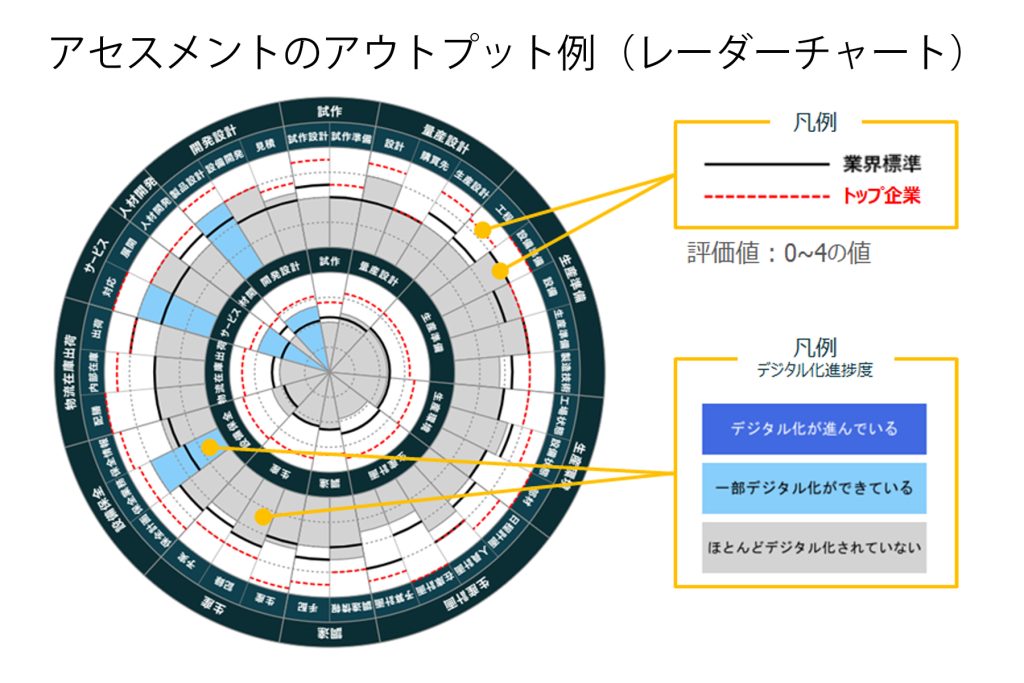
生産部門へのヒアリング/調査やトップインタビューを通じ、以下の主要問題が明らかになりました。
・設計と製造を含む生産領域において、部門間の連携にさらなる工夫の余地がある
・業務が属人化しやすく、情報の一元化や明確化に課題があり、生産計画の精度に影響する場面があった
・自社製品の収益性や市場動向に関する分析が、より深掘りできる余地が残されている
こうした中でも特に、生産管理において柔軟な対応が求められる場面が多く、全体的な改善の必要性が浮き彫りとなっていました。そこで、生産計画の立案業務を起点に製造/物流/営業といった各部門の情報整流化を行いつつ、最終的な業務デジタル化までの3カ年計画も整備しました。
生産能力の可視化・課題整理と、生産計画の標準化を実現
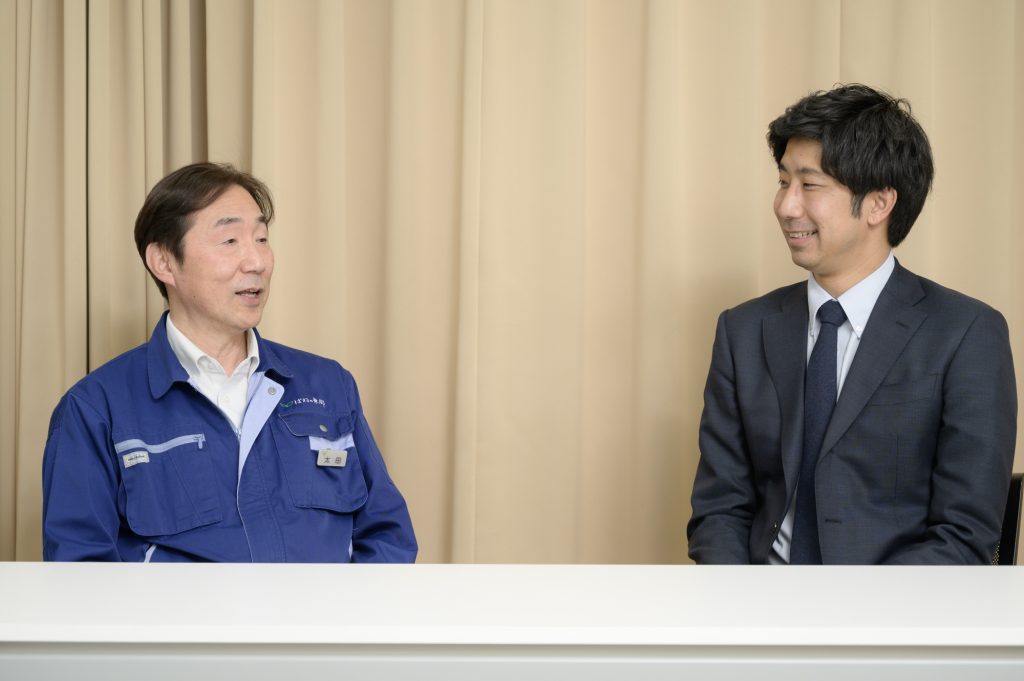
生産管理における問題として、以下の点が挙げられました。
・適正在庫数と受注予測数の精度に改善の余地があり、生産計画に対する調整対応が求められる場面があった
・生産計画に沿いつつも、現場での臨機応変な判断が必要となるケースもあり、進捗把握にやや難しさがあった
・一部の設備については、生産能力の現状や必要数の把握に不明瞭な点があり、投資判断の精度に影響を及ぼす可能性があった
このような状況で生産の混乱が発生し、現場では負荷の高い時期が長期間続いていました。また遊休設備も多くリソースの有効活用ができていない状況でした。
在庫管理においては、多様な特徴を持つ品種を生産しているにもかかわらず、多様な品目に対して一律の在庫ルールが適用されていたため、品目によっては在庫が過剰になったり、不足による特急対応が発生したりするケースも見られました。そこで、受注から納品までのリードタイムと年間生産量に基づいて製品を分類し、品番ごとに適切な在庫設定を行いました。
また、受注予測についても、従前の受注予測パターンから大幅に拡充をしました。これにより在庫の適正化が進み、受注予測の誤差は45%から15%まで改善する見込みが立てられました。その結果として、在庫削減によるキャッシュ創出に加え、イレギュラー対応の工数の削減も想定効果として挙げられます。
さらに、設備別の生産能力が曖昧である課題もありました。そこで、保全・段取り・不良などの停止ロス要因を整理し、本来持っている設備能力を算出し必要に応じた設備増強判断も正確に行うことが可能になっています。
これらの取組みで精度向上した生産計画をベースに、高負荷な時期を事前に予測し、1か月単位で負荷の平準化をする仕組みも整備してきました。その結果、同等の設備稼働時間でも残業時間が減り、現場の負荷も大幅に軽減される目途が立っています。
また属人化していた生産計画業務について、ベテランのノウハウと新たに整備した作業を手順書として作成することで、効率的な運用体制を構築。さらに、前述の生産能力の再定義とあわせて今後のシステム化に向けたデータ整理も進みました。これにより、新たに計画業務に従事する社員も標準手順書を活用することで、スムーズに業務を習得できるようになっています。
共通のゴールへの納得感が「改革に向かう姿勢」を作る
生産計画業務の改善、受注予測の強化、在庫の適正化によるキャッシュ創出といった成果に加え、プロジェクトの進行に伴い、副次的な効果も生まれました。それが、部門間の連携強化と組織内の意識改革です。
これまでの東郷製作所では、全社的な取り組みを進めるうえで、部門間での歩調を揃えることが難しい場面もありました。背景には、各部門がそれぞれの視点で最適を考える中で、意見のすり合わせに時間を要するケースがあったためです。
「以前は、それぞれの立場で改革の目的や必要性への理解が十分に行き届かず、取り組みの意義が伝わりにくい場面もあったように思います。しかし、今回のプロジェクトでは『この活動を進めることで、仕事が大きく変わるのではないか』という期待を持つようになり、会議での議論もより前向きなものへと変化していきました。担当者レベルでも意識が大きく変わり、積極的にプロジェクトに関わるようになりました」(太田氏)
こうした変化が生まれた要因のひとつが、「共通のゴール」の明確化です。従来は各部門の視点で議論が行われることが多く、全体の方向性が見えにくい状況でした。他部門の改善活動が、結果として全社的、あるいは自部門の改善につながるというイメージが持てなかったのです。しかし、今回のプロジェクトでは、オーツー・パートナーズが全体を俯瞰し、最終的なゴールを明確に示したことで、それぞれの部門が互いの業務への理解を深め、共通の目標に向かって進める環境を整えました。
大規模な改善活動には多大な労力が伴います。成功への明確なイメージや納得感がなければ、プロジェクトを前進させる力は生まれません。今回は最終的なゴールから共通認識を深める役割を社外から支援し、プロジェクトを推進していきました。
データ経営と生産連携強化による市場変化へのクイックな対応が企業成長を加速させる
現在、プロジェクトは当初計画した3年のうち1年目が完了した段階ですが、生産連携強化の取り組みと並行して進めているのが、データ経営の推進です。
従来は、製品ごとの収益性管理や市場分析について、より踏み込んだ取り組みを行うことで、CN(カーボンニュートラル)対応やEVシフトといった市場の変化にも、より柔軟かつ迅速に対応できる可能性を残していました。そこで、売上・原価情報の集約ルールを1から見直し製品ごとの収益性を可視化する取り組みを進めています。さらに、製品ごとの収益性データと市場分析を組み合わせることで、営業・生産戦略への活用を目指しています。
これまで、市場変化があるたびに経営戦略や体制の見直しを行ってきましたが、対応の遅れにより一時的な業績の落ち込みを避けられないケースが多くありました。ある変化に対応し、成長軌道に乗ったところで、また新たな変化に直面し、対応に追われる—。この繰り返しを防ぐためにも、市場競争が激化する中で、迅速かつ適切な意思決定が求められます。
生産連携の強化とデータ経営の高度化を通じて、これを実現し、成長の加速を図るべく、現在もプロジェクトが進行中です。今後は、さらに高度な分析モデルの構築を進めていきます。
また、全社的な業務改革の第一歩として生産計画範囲が完了したことで、今後は物流・保全・調達などの部門にも改革の幅を広げ、3年目には変革した業務に適したシステムを導入する予定です。この「業務変革を果たしてからのデジタル化」こそが、DX成功の鍵となるのです。
目指すのはタイムリーに社会に貢献する製品を生み出し続けること
太田氏に、今回のオーツー・パートナーズの支援についての評価を伺いました。
「(本プロジェクト担当PMの)林さんをはじめ、現場でのリーダーシップが素晴らしいと感じています。また、モノづくりに精通し、製造業の人間の気持ちをよく理解している点も非常に良かったですね。俯瞰的な視点でプロジェクト全体を把握しつつ、現場の状況を深く理解し、メンバーとも率直に話をしてくれた。それが、多くのメンバーを前向きにさせた要因だったと思います」(太田氏)
最後に、東郷製作所の今後の展望について伺いました。
「今後は、特に製造とデータの連携を強化していきたいと考えています。お客様が必要とするものをタイムリーに生産し、社会に貢献できる開発品を継続的に生み出していきたいですね。また、これから先、人材確保の課題がますます大きくなることが予想されます。そのためにも、デジタル化と業務の最適化を徹底し、業務の効率化と高度化を目指していきます」(太田氏)
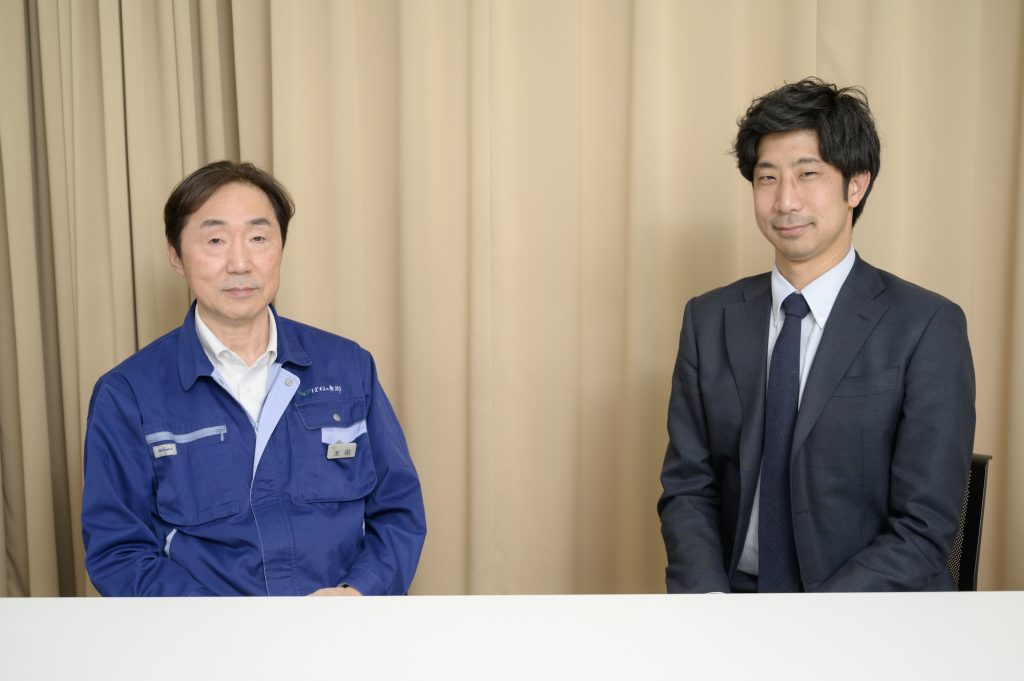
大企業から中小企業、地方のスタートアップ企業まで、
幅広い支援事例から代表的なものを紹介いたします。
他の事例はこちら
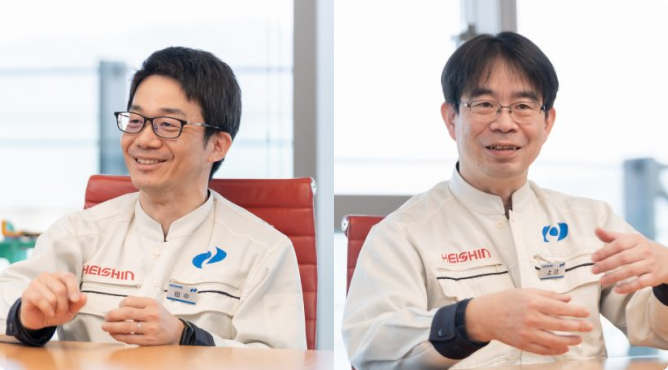

業種 |
|
---|---|
支援内容 |
|
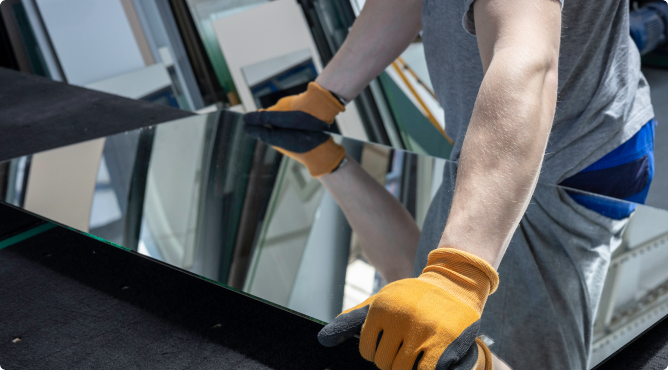
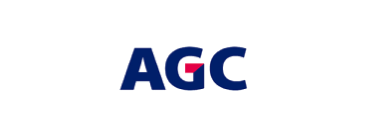
業種 |
|
---|---|
支援内容 |
|
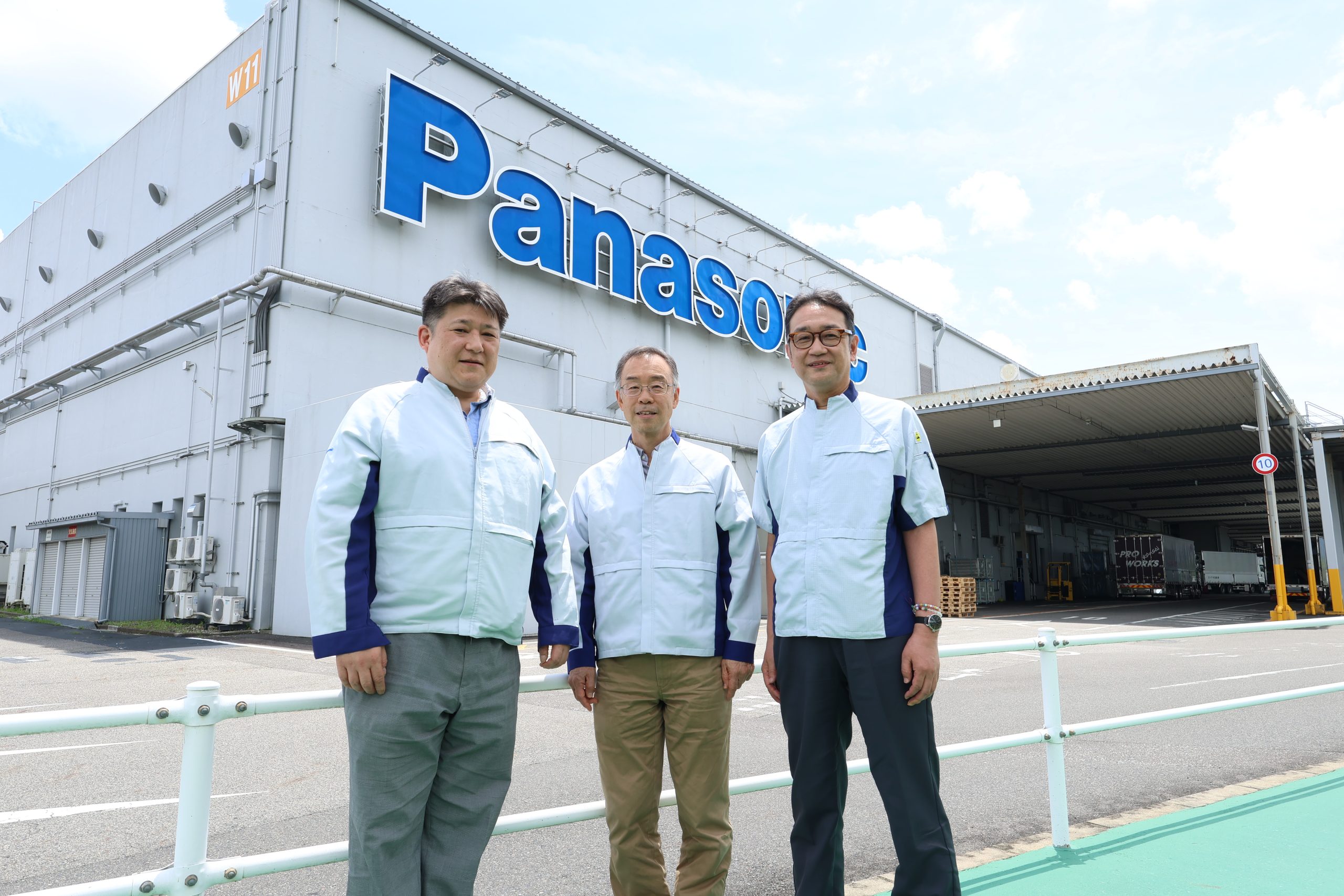
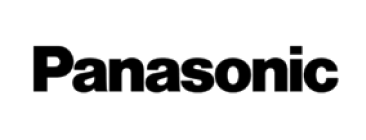
業種 |
|
---|---|
支援内容 |
|